Heat Pumps
Click on the manufacturers listed below to go to their websites for viewing the many products in stock at DESCO Energy. Click on the underlined blue text for areas of more explanation in our website. For assistance call us toll free at 877-265-9764 or email info@descoenergy.com
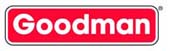
Heat Pump Systems
Split Systems
15+ Seer
14 Seer
13 Seer
Air Handlers
Variable Speed
Standard Multi-Speed
Coils
Cased Coils
Accessories
Linesets
Disconnects
Thermostats
Mini-Split Systems
Packaged Systems
To get started click on any of the blue words in this introduction for a more complete explanation. DESCO Energy and SEER Solutions for Energy Efficient Results will guide you through the entire process of sizing and selecting the most efficient system for your house or business. We recommend all potential customers review all the information provided in our Getting Started and Solutions section of the web site. When you're ready an Online Sizing Form using Manual J is provided to complete with detailed construction and sizing of your home including location and insulation values to determine the exact heating and air conditioning requirements of your building. This valuable information provides the necessary information to accurately select and size the heating and air conditioning system that's right for you.
Heat Pump systems are rated for efficiency and capacity. Efficiency is rated in levels of Seer or Seasonal Energy Efficiency Ratio for cooling and HSPF or Heating Seasonal Performance Factor for heating. Capacity is rated in BTUS or tons. Heat pumps are sized based on the cooling load requirement of the house. Today's new more efficient systems are built better and they last longer. There have stronger warranties and more features than ever before to help you save energy. Many existing air conditioning systems continue to use the reliable R-22 refrigerant while newer more efficient systems use the newest R410a refrigerant commonly referred to as Puron. R410A refrigerant systems now come in two stage compressor operation providing better humidity and temperature control. While the newest state of the art compressors provide variable modulation to vary capacity for a whole range of temperature and humidity conditions. Other energy and comfort features available are variable speed blowers to maintain constant air flows, increase dehumidification, reduce and eliminate blower noise and reduce energy consumption 85%.
DESCO Energy will put together a complete package for your specific application including the new energy efficient fiberglass duct systems. Only here can you find a complete package including the duct air handling system designed and precut for your needs. Fiberglass duct board provides many features which surpass using more costly sheet metal ducting. Features and benefits of fiberglass duct board include easier installation, higher insulation, quieter attenuating the transmission of any noises, almost zero air leakage and thermal losses with no condensing compared to sheet metal's average 25% energy losses, safer with no sharp razor edges to deal with, and much easier to fabricate and assemble with little expertise or costly specialty machinery or expensive hand tools to purchase. DESCO Energy will design a complete duct system or size any air handling system at no extra charge with the purchase of a complete heating and air conditioning system.
Whether your needs are for your home, business or industrial applications DESCO Energy can provide the best system for you at wholesale pricing. And we'll show you how your new system may be eligible for Tax Credits under the New Energy Bill.
Annual savings based on 36.000 Btu unit, 1500 cooling load hours, and .08/kwh. Actual savings may vary depending on climate conditions, energy rates and patterns of usage.
|
 |
|
On January 23, 2006 all HVAC manufacturers have been mandated to only produce air conditioning systems with a minimum 13 Seer or Seasonal Energy Efficiency Ratio. Heat Pumps are also mandated for the same air conditioning efficiency with a minimum 7.7 HSPF or Heating Seasonal Performance Factor. 13 Seer line will be the lowest grade equipment produced with the lesser of all warranties. The 2006 Energy Tax Bill will offer tax credit rebates effective for equipment installed on or after January 1, 2006. A $300 rebate will be offered for split system air conditioning systems of 15+ Seer or packaged systems with 14 Seer. There are also tax credit rebates of $50 for variable speed blower motors. Heat pumps with the same 15 Seer air conditioning and 9.0 HSPF are also eligible for a $300 rebate.

If you are installing a split air conditioning system in combination with a gas or oil furnace please refer to our Dual Fuel Systems section under Products subsection.

The most common configuration, a split system is designed to work efficiently for cooling in any climate. Split systems have two main components, the outdoor section (e.g. air conditioner) and the indoor section (e.g. coil and furnace). These two components work together to provide top performance, maximum efficiency and comfort. |
|
Packaged systems are designed to heat and cool your home. Your packaged unit may consist of either a heat pump or air conditioner; or a combination furnace and air conditioner called a gas/electric packaged unit. |
Heat Pumps
Below are the items required when installing a heat pump. The first item in a split system application is the outdoor condensing unit. Condensing units are rated in capacity and efficiency. The resulting efficiency and capacity are determined in by the correct matching indoor coil or air handler. The capacity ranges from 1.5, 2, 2.5,3,3.5,4 and 5 tons. Efficiency can range from 10 Seer to 18 Seer for cooling and 7.5 to 9.5 HSPF for heating. 15 Seer and 8.0 HSPF and higher efficiency units use 2 staging and the newer R410A refrigerants. As the efficiency and the capacity increases so does the size of the unit. Important to note the outdoor unit must be at least 18" from any walls and clear of any overhead projections for proper air movement.
A split system installed in conjunction with a furnace will need an indoor coil and this is referred to as a dual fuel system. DESCO Energy only stocks cased coils meaning there is an insulated wrapper around the coil. If your specific application is to place the coil inside the existing plenum simply remove the wrapper supplied. Removing the wrapper only takes 5 minutes. The difference in cost between a cased and uncased coil is only 4 dollars so rather than stock two different types of coils we only stock cased coils. Coil selection is based on the manufacturers specifications and not on the size of the outdoor unit. For example a high efficiency three ton outdoor unit may require using a 5 ton indoor coil. Today's higher efficiency equipment requires larger coil surfaces on both the indoor and outdoor units. Another factor affecting coil selection is the size opening of the furnace. coils need to be selected to match this size as closely as possible while still maintaining efficiency within the manufacturer's specifications. And another factor affecting coil selection is where you are located. Higher humidity climates require the smaller coils offered by the manufacturer. The smaller coil will produce colder coil temperatures resulting in better dehumidification. For the above reasons it is best to have a NATE certified technical support team member select the matching coil that is best for your specific requirements.
If the split system requires a separate system not involving a furnace there will be an air handler required. The air handler provides both the indoor coil, blower and electric heating element. There are two basic types of air handlers. The main difference between the air handlers is that one will use a standard PSC or permanent split capacitor motor with multi speeds. The best air handler is that using a variable speed blower which maintains a constant air flow and provides many other features and energy savings benefits. Variable speed blowers on air handlers use less energy, provide better dehumidification, provide almost silent operation of the motor with silent start and stop and can be programmed for different air flows based on the requirements of the needs of the specific application. Variable speed blower motors use less than 1/5 the energy of standard blower motors. And the cooling coils come with TXV control of the refrigerant for more exacting and efficient cooling control.
Electric heat strips are referred to as back up heat, emergency heat and auxiliary heat. The electric heat used is all one in the same. The electric heat is sized for the full heating requirement of the house without the capacity of the heat pump taken into consideration. Heat strips come in various capacities measured in kw or kilowatts. The heat output depends on the electric voltage supply at the house. Some areas use 208 volts while others use 240 volts. Heat kit kw is rated at 240 volts and areas with 208 supply power will have a 13% reduction in kw and subsequent heat output. The basic formula of 3.4 btus per watt is the sizing factor for determining the heat required. Heat kits come in 5, 8, 10, 15, 20 and 30 kw packs. Circuit breakers are supplied with each heat kit provided as required by code. Each 10kw of heat requires a 60 amp 240 volt breaker and produces 34,000 btus.
The next item on the list of pictures shows a light condenser pad. Pads are used in lieu of concrete pads for placement of the outdoor condensing unit. In many instances it may be easier to install a condenser pad with a 5" stone base or no base at all. Where there is a slight grade for the location of the outdoor condensing unit or movement of the soil due to heavy rains or freeze thaw conditions it is highly recommended to use a 4" concrete base with 4" stone base. Remember the outdoor unit needs to be located at least 18" from any exterior wall and free of any overhead obstructions.
Risers are required to be placed under the outdoor unit at the four corners. The purpose of the riser is to elevate the outdoor unit so that condensate can drain freely and clear of the unit. Also risers provide protection against snow accumulation. Risers should be considered essential for moisture removal in defrost cycles in every heat pump application whether or not the previous system had them. Risers come in 3,6 and 12 inch heights. Certain codes require the use of 12" risers for flood protection as well.
The next item is the refrigeration lineset that connects the refrigeration system together from the indoor unit to the outdoor condensing unit. Keeping this length as short as possible is important for maintaining maximum efficiency and performance. The standard linesets come in 30 and 50 foot lengths and in three different sizes. With the small line at 3/8" O.D. copper called the liquid line and the larger line called the suction line with insulation the sizes range from 3/4", 7/8" and 1-1/8" O.D. copper. Longer lengths are available. The size of the suction line is determined by the capacity of the system as well as the length of tubing lineset involved. 3 ton and over systems use a minimum 7/8" suction tubing for 30 feet or less. For 3 ton and over with 50 ft. lengths of linesets they would use 1-1/8" suction line sizes.
If this is a replacement system and you've chosen not to replace the lineset because it is too difficult to replace a filter drier for removing harmful acids and debris and moisture must be installed. It is highly recommended to always replace the lineset when replacing any air conditioning or heat pump system so you are assured everything is clean and fresh and no residual contaminants will infect the new system. If not a suction and liquid line drier should be installed of the type for removing acid, moisture and filtering.

For a decorative outside professional appearance a lineset thimble can be used to enhance the penetration required for the lineset. Thimbles are available in round and rectangular design.
The electrical whip and disconnect are the next items for the outdoor unit. For every outdoor unit there needs to be an electrical disconnect within sight and reach of the outdoor unit. This is required by all electrical codes in allinstallations. Most new codes require the use of an electrical disconnect with an electrical 110 volt receptacle attached and ground fault protection or GFI. Standard disconnects come with fused or non fused. It is highly recommended to follow the electrical codes in your area. If a GFI type disconnect is required this can also be handy for any service or another outside source for a plug in connection. At the very least a fused or breaker type weather proof disconnect should be used. The ampacity or size of the disconnect should be no less than that required under the HVAC manufacturer's specifications. Keep the electrical disconnect as close to the outdoor unit as possible. The electrical whip is a plastic sheathed protective tube with electrical copper wiring inside to connect electrical power from the outdoor unit to the electrical disconnect. Electrical whips come in one size and rated at 240 volts at 60 amps at 6 feet in length.
The thermostat is the next item required. Thermostats come with many different features and programs today. The newest hi tech thermostats provide a wide array of energy saving features such as every day of the year programming with daylight savings features to monitoring hours of operation with reminders for when to change filters. Intelligent energy recovery is essential tot he energy savings accompanied by the use of a heat pump. By slowly raising temperatures at different time periods depending on time required, intelligent energy management will raise indoor temperatures whenever practical without the use of the electric back up heat. In addition they can also control humidity for humidification while monitoring outside air conditions to prevent condensation of walls and windows. A few can actually control variable speed motors to reduce the air speed for a true dehumidification cycle while others will lower the thermostat cooling setting to provide more dehumidification. Some thermostats are internet ready where they can also be monitored or adjusted over the internet or phone or monitor conditions to send alarms. All this with many more functions or to the simplest electro mechanical thermostats are available.

Outdoor thermostats are important additions to heat pumps to provide a changeover in accordance with the balance point. The balance point is where the heat pump capacity due to lowering of efficiency is no longer sufficient to provide the required amount of heating. The balance point can be anywhere from 37 to 23 degrees outside temperature.
Electrical thermostat wire needs to be considered for wiring from the thermostat to the indoor air handler or furnace and then to the outdoor condensing unit. Remember thermostat wiring should never be installed inside conduit or plastic sheathing with power wiring. The new hi tech thermostats can require up to 8 conductors from the thermostat to the air handler or furnace while thermostat wiring from the indoor furnace to the outdoor unit will generally require no more than 3 conductors. When running thermostat wire make certain to always run one or two more leads than required for future changes or a broken wire that may occur.
Vibrations pads and corners are used when the indoor air handler or furnace needs to be mounted to raise the level of the indoor unit or to attenuate noise transmission. Corners are recommended when the air handler or furnace is placed in an upright position on a floor with central return. Vibration pads are primarily used in horizontal mounting positions of the indoor air handler or furnace to attenuate noise transmission. Either corners or vibration isolators are very inexpensive and are worthwhile investments.
Condensate traps need to be installed in the drain lines of every air conditioning system. Without the use of a trap the negative air pressure inside an air handler or the positive pressure on the coil of a furnace block the natural flow of condensate and result in overflowing of water from the coil. But condensate traps accumulate debris and need to be cleaned at least once annually and in more hot and humid climates once per month. Traps should be installed with screw type unions where they can be easily removed and cleaned. Pouring hot water down the condensate line can be somewhat effective in checking the operation of the trap. But heavy accumulation will inevitably result in build up that blocks the trap. Being able to remove and effectively clean the trap with warm running water is the best solution. Traps and condensate lines should be a minimum of 3/4" PVC tubing. Copper and steel drain lines should be avoided as they will clog up faster and are more difficult to keep clean.
When a drain access is not readily available such as in a basement or first floor application the use of a condensate pump may be required. Condensate from the air conditioning system is drained into the pump reservoir where a float energizes operation of the pump. Alarm contacts are also provided to deenergize the air conditioning system in the event of pump failure. 3/8" clear plastic tubing is then piped outside or to a local sewer drain.
The auxiliary drain pan is required when placing an air handler or coil in the horizontal position. Eventually condensate traps
will clog unless someone is extremely diligent on constant maintenance. So the attitude should always be when and not if it clogs what damage will occur? In almost all instances horizontal applications are above in an attic area where a condensate trap is not easily accessed for routine maintenance and easily forgotten until they clog. By having an auxiliary drain pan the condensate then flows safely out of the coil on to the auxiliary drain pan and drains safely past the clogged trap. There are also auxiliary drain pans available for vertical or upflow applications. Clogged traps can also result in damaging expensive hardwood flooring or ceilings and floors beneath.
Another protective highly recommended device is the drain alarm. Drain alarms come in two possible applications. One such trap shown can provide an alarm as well as deenergize the air conditioning system until the trap can be safely cleaned. Another senses the accumulation of water build up in an auxiliary drain pan and provides the same protection with an alarm and deenergize the air conditioning system.
For proper indoor air quality the air system needs to be properly filtered either using a high media or electronic air cleaner. The high media filter is the most recommended because of higher reliability and visual evidence of proper operation. Electronic air cleaners continue to be less reliable and more expensive to maintain and purchase. Hi Media filter protection is essential to maintaining clean efficient operation of any HVAC system.
In humid climates where mold and mildew are a constant problem the use of an ultra violet lighting system needs to be considered. Ultra violet lighting systems provide the only certain method of controlling and eliminating build up of damaging and harmful fungus and mold spores on wet air conditioning coils.

Protective devices should also be considered for the longest most reliable system performance. If the air conditioning system you are selecting will be operating under unusual circumstances then a low ambient kit should be considered. Low ambient kits provide system protection and efficient operation when the outside temperature falls below 65 degrees. This type of application occurs in restaurants, computer cooled areas and offices with high heat loads. It can also occur in residential applications where internal areas only are being cooled and the cooling is operating beyond it's design conditions. A low ambient kit cycles or varies the speed of the outdoor fan to maintain a consistent pressure in the refrigeration system essential for efficient operation and protection of the compressor.
Another protective device the hard start kit is used when there is frequent operation of the air conditioning system and/or when there are low power voltages or brown outs. Lower voltages or situations where the refrigeration pressures do not have sufficient time to properly equalize will cause the compressor motor to stall and trip on it's internal overloads creating extreme stress on the motor. Systems using TXVs should also consider the use of hard start kits where undue time is needed for the system refrigerant pressures to equalize. An example of a stalled condition imposed by people can occur by turning the thermostat setting up and down several times quickly. This will cause the compressor motor to stall and trip on it's overloads. With a hard start kit this problem is eliminated and provides extra energy to the compressor motor to overcome problems of insufficient power or rapid cycling substantially increasing compressor life.
A new protective device is also available to monitor and provide added protection to the Copeland Scroll compressors. A very important module which is only available from certain HVAC manufacturers on their highest efficiency models. At the very least the compressor monitor will reduce unnecessary compressor replacements that result from incompetent technicians and contractors misdiagnosing problems. Remember Copeland reports over 35 % of compressors returned under warranty have absolutely no defects and the other 60% are returned with defects that could have been avoided due to improper installations. How many compressors are condemned with no defects out of warranty? You can help avoid this costly mistake and problem as well as provide better compressor protection with the compressor protection module by Copeland.

For packages unit installations the risers, disconnect, whip, electric heat kit, high media filter, thermostat and outdoor thermostats listed above should be the main considerations.
Heat Pump Installation Considerations
If you are installing a split air conditioning system in combination with a gas or oil furnace please refer to our Dual Fuel Systems section under Products subsection.
The main physical difference between an air conditioning system and a heat pump is this component, the reversing valve.
The reversing valve reverses the flow of the refrigerant to provide normal air conditioning in the summer and reverse the flow to provide heating in the winter. Heat pumps require special design considerations when making a design for installation. Duct sizing and layout are critical and must be more precise than for any other type of system.
If you are installing a split air conditioning system with a separate air handler where no systems or ducting exists you will first want to determine the location of the air handler and outdoor condensing unit. An outdoor unit is only half of a split-system. The air handler is the inside half of the system. Working in tandem, outside and inside units must be matched in size and efficiency for best results. Failing to replace an indoor unit, or mismatching components, can significantly undermine a new air conditioner's or heat pump's performance. An air handler consists basically of a blower, an inside coil, and optional auxiliary electric heating strip. In the cooling mode, as air flows over the indoor coil, heat and humidity are drawn out. It's the air handler's job to then circulate conditioned air throughout the house. Ultimately, performance varies as a result of the blower motor choice.
If your application is in a single story home the best choice for locating the air handler is in the attic area. By locating the air handler and ducting in the attic the cold air will fall from ceiling diffusers and provide excellent comfort. If there is no attic available or accessible the air handler and duct system can be run in the living area. The duct system can be installed in a bulkhead which can later be enclosed in drywall. A last resort would be to locate the air handler and duct in a crawl space. The air handler could also be located in the living area while the duct work is in the crawl space area. The problem associated with this type of installation is the simple rule that cold air falls and comfort levels will not be as satisfactory. Floor feeding registers for air conditioning always produce comfort problems as the room air at a 6 foot level is always 8 to 15 degrees warmer than the floor temperature. Air handlers should not be located in garages that are not living areas or have ducting supply or return air form garage areas. Garages have a 2 hour fire code separation in most homes built since the late 1980s. The purpose of the fire block is to prevent a fire form spreading from the garage to the house. Even if your house does not have this fire separation and even if the existing air handler or ducting is located in the garage area, the replacement system should not violate this valuable fire protection. A fire ignited in a garage with a tank of gas is like a bomb and will move even faster if fanned by an air handler or can easily migrate through the house via a duct system. Further if there is a fire and subsequent investigation determines the spread of the fire was due to a code violation the insurance company will generally not honor the claim especially when that violation was a result of a homeowner's do it yourself project.
On a two story home life becomes more challenging when installing any type of ducted heating and/or air conditioning system. Certain parameters need to be followed in order to make the best decision. SEER - Solutions for Energy Efficient Results has established guidelines for installing any forced air HVAC system on a two story house. First a determination needs to be made if a single system or two systems should be used. Before you cringe about the idea of two systems read this first. Many times two systems are less expensive to install compared to one system with zone dampers. With two systems there is less labor and material for ducting. There is also less labor installing two systems over one. There is no recommendation being made that all two story homes should have two systems but there are guidelines for when they should be considered:
If the total cooling load for the house is 3 tons or more.
If your house is over 1,800 square feet.
If there is an open stair case to the second floor.
If there is a vaulted ceiling to an open second floor area.
If the existing system provides intolerable temperature variations between floors
If comfort is a priority.
If maintaining consistent temperatures is important.
If maximum energy savings are your goal.
If having at least one operable system eliminates the need for an emergency service call if the other system fails.
If you want cooling on one floor without having to overcool the other floor.
If you want heating on one floor without having to overeat the other floor.
If having cooling on one floor and heating on the other floor when required.
If there are substantial differences in construction style from one floor to the other - Eg. First floor has large glass areas and vaulted ceilings and second floor has lower ceilings and low glass exposure.
The most important part of any air conditioning system beyond the equipment is the duct or air distribution system. SEER - Solutions for Energy Efficient Results Strongly recommends the use of fiberglass ducting. Fiberglass duct board is the easiest most efficient reliable product on the market. In comparison to sheet metal ducting fiberglass ductboard is less expensive and requires less labor to install than equivalent sheet metal ducting with fiberglass insulation. Fiberglass is more efficient because it doesn't leak air and is totally silent. Fiberglass attenuates noise created by air movement and noise created by the motor and blower. Sheet metal ducting accentuates noise making for a louder operating system. But you can't find fiberglass ducting everywhere.
Benefits Of Fiber Glass Air Duct Insulation Products In An HVAC System

As key components of a well-designed, operated and maintained HVAC system, fiber glass air handling insulation products improve the overall quality of the indoor environment. These materials not only provide cost-effective delivery of indoor environmental quality, they conserve energy, maintain air temperature, and control noise and condensation.
Energy Conservation
The insulating role of fiber glass duct board, duct wrap and duct liner has become even more important with the increased emphasis on ventilation. Increased ventilation requirements place more demands on a building's energy source. The importance of energy efficiency is increasing in terms of overall energy conservation and the affordability of increased ventilation.
Consistent Air Temperature
By reducing the heat transfer across the duct system, fiber glass insulation products allow a building's HVAC system to deliver conditioned air at design temperatures. Consistent air temperatures mean increased comfort for building occupants without over-taxing the energy source, while maintaining lower energy costs.
Noise Control
Without fiber glass insulation products, the acoustical environment of mechanically conditioned buildings can be greatly compromised. Fiber glass duct board and duct liner reduce the transmission of HVAC noise through the duct system, such as expansion and contraction of steel ducts (popping and cracking), air turbulence, etc. Fiber glass acoustical insulation also reduces noise transfer (cross-talk) from one room to another through the ducts.
Condensation Control
Fiber glass duct liner, wrap and board help control condensation in air conditioning duct systems, reducing the opportunity for microbial growth. Condensation will form on bare sheet metal air-conditioning ducts at any point at which the duct surface temperature reaches the dew point. The moisture may remain in place or drip, causing moisture damage and creating a potential for microbial contamination. Fiber glass insulation corrects this problem by reducing moisture occurrence, thus eliminating a precondition for microbial growth.

House Additions
If you are planning to add an addition or the addition is already completed, treat the addition area as separate. Additions are almost always with higher insulation value and more energy efficient than the main part of the house. As a result the cooling and heating load requirements for these areas will be entirely different than the main part of the house.
To properly provide comfort to any of the above conditions a heating and/or cooling system must have zone dampers with proper control. The zone dampers or zoning will also require the dampers to either bypass the extra air back to the air handler when closed or a two stage heating and/or cooling system or both. Two stage air conditioning systems and zone damper systems are expensive. In fact so much more the additional costs are more than two separate systems. Two stage systems with zone dampers and a long duct system that stretches to cover all areas takes more space, requires more materials and labor and adds to the overall costs. Zoning systems without two stage compressors for the cooling system are a perfect recipe for premature equipment failure. Air conditioning systems require critical constant air flows. Typical zone dampers simply open and close air supplies with no regard to the effect on the overall air capacity required. For example a 3 ton air conditioning system requires 400 cfm - cubic feet of air flow per minute per ton or for three tons - 1,200 cfm. Zone dampers controlling an equally proportioned two story house would be placed to block air flow to the first floor when no cooling is required in that zone. That would reduce the air flow by 50 to 60% in the main system or reduce air flow to 600 to 720 cfm of air. That reduction in air flow would cause serious harm to the air conditioning compressor and result in excessive noise in the air diffusers in the second floor as the extra air capacity is attempting to be forced out fewer air diffusers. A two stage air conditioning system would automatically reduce the air flow as required when the zone dampers were closed. The damper control system would send a signal tot he air conditioning system to cause this reduced air flow and lower operating speed of the compressor thus causing no harm. This is just one example of why zoning and two stage air conditioning systems are a better more expensive choice than one single stage air conditioning system. But the ultimate less expensive solution is two separate systems. The other advantage to using two separate systems on two story applications is the ability to run different ducting systems. The first floor system is usually floor fed while the second story system is ceiling fed. Stratification that migrates from the first floor heating system will then have less effect to the second floor conditions. The second floor air conditioning will also migrate to the first floor with a minor effect.
Most homeowners rarely consider the need for two systems nor the benefits. Usually the thought is to accomplish everything with a single system. But realizing stratification and the role it plays in comfort there are many huge beautiful houses with large vaulted ceilings and open stair cases where dual systems or zoning was never considered. The end result is a house that is so unbearable the occupants can't sleep comfortably or to accomplish proper comfort on the second floor the first floor becomes unbearable.
If your application is new construction or renovation now is the time to consider all possible options for comfort and efficiency. After the house is completed the cost to correct HVAC mistakes becomes very pricey.
After a determination has been made for the size and number of systems required and the location and layout of the air handlers is selected, the next process is to locate the outdoor or condensing units. The closer the distance the air handler is to the outdoor unit, the more efficient it will operate. The vertical distance has the greatest impact on efficiency. Typically line sets for connecting the refrigerant lines are 30 feet and 50 feet. It is strongly recommended to keep the line set as short as possible and not more than 75 feet. Location of the outdoor unit should also consider the solar effect. Placing an outdoor unit in direct sunlight is the least favorable of all locations. An ideal location for an outdoor unit should be placed no closer than 18" to the wall of the house with no obstructions overhead and on a north wall less than 30 feet from the air handler. That would be a perfect location in a perfect world. Now if the decision to place the outdoor unit 70 feet away to simply locate away from the solar gain would not be the best decision. However of you live in the hot dessert conditions similar to Arizona, placing the outdoor unit out of the sun would be a top priority.
After the indoor air handler and outdoor unit have been properly located the next step is to layout the duct design. Ducting and it's design can be found in our Product subtitle. If you are having difficulty laying out the duct design or would like a review of your design or existing system, DESCO Energy provides a basic layout and sizing of any duct system upon purchase of a heating and/or air conditioning system. We understand that sizing and design of duct systems can be overwhelming so we will take that problem away at no charge at your request.

Homeowners sometimes request a complete review, sizing and selection and layout of the system. Again we will provide all these services to you. Those services are part of what we do for every customer that requests them.
Selecting the right system with the best efficiency. Realize you're already way ahead of the process of your heating and air conditioning system by making it a do it yourself project. What most homeowners want is the best value for their money. After all that's the motive behind do it yourselfers. Do it yourselfers want to save as much money as possible but not at the expense of having shoddy equipment or a shoddy installation.
Packaged units generally lack many of the higher efficiencies and features of split systems. For most homeowners packaged units and accompanying exposed ducting is unsightly and requires constant maintenance. Most packaged systems are usually used in areas where labor and trained installation technicians were difficult to find. Rarely are packaged systems used in new construction unless the design of the house lends itself for an easy packaged installation. The ease is a result of being able to place the ducting under the crawl space and the unit is designed to sit on a slab outside the house in a location not readily viewed. Packaged systems in residential applications are usually installed on one story homes due to the ducting restraints.
Packaged units are usually offered in two efficiency ratings from most manufacturers, the minimum and one step above. Packaged systems are easier to install but generally have a shorter life expectancy. We strongly believe the shorter life expectancy is due to improper design and installation of packaged systems. Many times homeowners in the attempt to save as much money as possible will purchase a packaged system to avoid the use of a licensed professional installer. Without any outside assistance the duct system is installed without proper sizing and distribution and with insufficient duct insulation. These factors are sufficient reason why packaged units have such a high failure rate. The installation also becomes a less than satisfactory job and the net result is short life expectancy. Packaged units can work well and have proven reputation of excellent service and longevity on commercial applications on rooftop installations. Perhaps the reason commercial packaged units last longer than residential systems is due to the fact that almost all commercial applications were designed and installed according to engineering standards. A packaged system can work for you if the unit is installed and designed correctly. And most importantly if the house design lends itself to the installation of a packaged unit which most do not.
If a packaged system wasn't in your plans then a split system of 14 Seer or more should be selected. 15 and 16+ Seer systems are mostly two stage and use the new R410 refrigerants. The outdoor units of today are larger than ever as large coil surfaces are required to achieve high efficiencies. Two stage systems are new and there is a premium price for these. As mentioned previously a two stage system with dampers is more expensive than two separate single stage systems. But there are other benefits to using two stage systems. The primary benefit is dehumidification. Two stage compressors are not going to be as popular in the Southwestern parts of the country as they will be in the North and Southeast areas. Dehumidification during light or milder summer days has always been a problem with air conditioning systems. Air conditioning systems are sized, selected and designed for the hottest summer days or an average of 95 degree outside ambient. At this condition the air conditioning system will operate for long cycle periods. A well designed system will operate at 70 to 75% of the time at it's design temperature. But most summer days are not at those temperatures. Because most summer days in most parts of the country are in the 80s the air conditioning systems are oversized for those days. The net result is the system only operates for 30 to 40% of the time. This shorter time period doesn't permit the system to operate long enough to allow the cooling coil to get cold enough to draw moisture out of the air. The net result is a house that produces a cool clammy environment. But if the system was smaller it would operate longer during those mostly milder days. And that's exactly what a two stage air conditioning system does, it operates for the same length of time as it did when it was hot outside providing enough time to satisfactorily create a cool dehumidified environment. The age old problem of cool clammy has been resolved with a two stage air conditioning system. And that's is what is so great about two stage air conditioning systems.
Heat Pumps
This section assumes you understand about proper sizing, efficiencies, problems in the HVAC industry and how to select a system. In addition there are other very important subjects which are of interest and necessity to properly selecting a gas furnace. If you haven't read the sections under SEER and Solutions we strongly recommend reading the information provided in those areas first.
Heat pumps are gaining in popularity today more than ever. With rising natural gas, fuel oil and propane prices heat pumps are more efficient and comfort making than ever before. Heat pumps are being installed in areas of the country never considered before including the northern sections of Canada.
Here's why most homeowners don't like heat pumps and why they receive a bum rap. As we state in all our product sections bad experiences and rumors never die in the HVAC industry. Like dinosaurs just when you think the public has a good impression of a product, some HVAC contractor from the stone ages rises up with an old persistent rumor that refuses to die. It's like discovering dinosaur bones. But these rumors are generally baseless. For each product section we go through the history of the products evolvement until today in an attempt to dispel myths and rumors of poor service evolved from yesteryear that don't have any basis about what is true and happening now.
At the beginning of the heat pump's first introduction in the 1970s was without doubt the worst product introduction in the HVAC industry. Heat pumps were like all new products sent into the market place without sufficient testing and research. Air conditioning compressors were used on heat pump applications. This resulted in 85% failure rates in the first three years. Control systems were so complex and involved they were more complex than the largest chillers used in industrial applications. Many manufacturers felt so much financial loss that some even went bankrupt through their heat pump operations. Manufacturers jumped in and then out and in and out again of the heat pump manufacturing so that on any given day nobody knew who was still in the heat pump business. But one manufacturer was an exception to all the others, General Electric. What General Electric did differently was not give up and never jumped out of the heat pump business. GE stuck with the problems and had field engineers in constant communication with their manufacturing engineers. Any problems discovered in the field by installers and contractors were immediately relayed back to the factory for correction. As well any suggestions from their contractor dealers were also heard and addressed. GE claims their success was due to the input from their contractors and that input helped them gain more knowledge, ideas and corrective actions than any other source. Dealers were required to have constant factory training as well as all their installation and service technicians. This commitment and close alliance with their dealers and required intensive training was unheard of before. But it paid off because by the 1980s General Electric was the number 1 name for heat pumps all across the country. Known for the most reliable efficient heat pumps and top notch contractors and service General Electric made a legend of itself in the heat pump business. By the end of the 1980s General Electric owned the heat pump industry having over 60% of the market share.
Until General Electric owned the heat pump business there were many other manufacturers out there doing a tremendous job of making a bad name for heat pumps. With products that had a life expectancy of 5 years or less these manufacturers were not doing the industry any favors. Compressors failed continuously to the point of major recalls by every manufacturer. Depending on the month it seemed as though every manufacturer was taking turns at having the biggest recalls in the late 1970s and early 1980s. Compressors had to be tougher with stronger motors and valves. Extra protection devices needed to be installed. Manufacturers were trying to constantly copy General Electric's design but not paying any attention to the most important factor, their dealer contractor relationships. Air conditioning systems had more tolerance to system installation imperfections but heat pumps were more critical. Adequate sized duct systems were not stressed to the dealers until so many failures continued to result from poor installations. Finally after continued equipment and manufacturing improvements weren't producing the longevity manufacturers expected, they decided to also copy General Electric's ideas on contractor training. Manufacturers began to require all dealers to have regular factory training and started to emphasize the need for correct installations and adequate duct sizing. Unfortunate for them it was too little too late. General Electric had such an impeccable reputation in the heat pump industry and at their peak held 80% of all heat pump sales. As other manufacturers improved the quality of their products and dealers and became more competitive General Electric began to lose market share. General electric has a unique business philosophy not known to many in the public. If GE can't dominate a field or product line they sell out and get out. So in the 1990s General electric sold all their product line except one to Trane. General Electric still dominated the PTAC or Portable Terminal Air Conditioner units industry which are used predominantly in the hotel industry. Through the wall heat pumps and air conditioners found in many hotels are the only remaining products still owned by General Electric because they continue to dominate that segment of the industry today.
What were the problems in the heat pump industry that have been resolved today? Compressor failures being the leading cause of heat pump failures were corrected with more durable compressors and suction accumulators that protect the compressors. As well more efficient designs with better quality products have also had an impact. Problems of blowing cold air during defrost operations and start up have been improved by better electronics and variable speed motors. Today's heat pumps are more simplified and operations are more standardized between manufacturers. Some manufacturers such as Lennox and Carrier continue to over design and engineer control systems without increasing overall longevity or reliability. For the most part manufacturers have made troubleshooting and diagnostics much easier today and less complex. Today's new ultra efficient heat pumps when sized and installed correctly have a 12 to 15 year life expectancy. When used with variable speed ECM motors heat pumps provide a level of comfort comparable to any gas furnace.
But the original problem of poor installations continue to plague the heat pump industry more than all other problems combined. Lack of manufacturers requiring dealer training today and incompetence have resulted in the worst overall contractor force in the history of the entire industry. Over sizing equipment and undersized duct systems, an epidemic problem in the HVAC contractor industry has a greater negative impact on premature heat pump failures than any other type system. Why? Heat pumps require very accurate sized duct or air distribution systems and proper sized systems because of the adverse conditions in which they operate. In other words there's not much room for error when designing and sizing a heat pump system. Gas furnaces, oil furnaces, boilers, radiant heating and hydronics all have a greater margin or tolerance to absorb errors than heat pumps. So contractors having poor designs and installations will have their greatest problems with heat pumps. Those problems are reflected as excessive warranty claims and repeated call backs and finally premature equipment failures. To counter the system problems these types of contractors revert back to digging up dinosaur bones and will point the finger at the manufacturer rather than themselves. They will tell homeowners about the problems of yesteryear with heat pumps as though it were today and/or the manufacturer. See more about this topic in Industry Problems at our Start Here subsection of our web site. This problem can't be sugarcoated and there's really no excuse for excessive warranty problems or repeated service calls or premature equipment failures in heat pumps. Heat pumps do and are lasting longer than 4, 5, 7, 8 or 10 years.
If the heat pump you have failed in 10 years or less follow the guidelines for proper sizing and selection in our Start Here subsection. Or if yours is a new installation you want to last the industry average of 12 to 15 years follow the same steps. Then realizing the minimum industry efficiency system is 13 Seer and 7.7 HSPF beginning in 2006 select a system at least one Seer point higher or 14 Seer to avoid the basic builder style system. SEER - Solutions for Energy Efficient Results recommends never selecting or installing any system at minimum efficiency levels. These are the cheapest of all equipment models lacking many features. To provide the cheapest pricing everything considered non essential is removed that provides proper protection or comfort and are referred to as the Builder's Grade Units. Incredibly these are the same systems installed on over 96% off all new homes regardless of the price tag. Why? Because potential homeowners will ask what manufacturer but rarely what efficiency system was installed. Frankly since all manufacturers use the same compressors, relays. controls, tubing, coil materials, metal and components it really makes little difference who the manufacturer is. Carrier for example the largest manufacturer has the worst consumer record of all manufacturers according to the Better Business Bureau website. Yet more homeowners have a false sense of security with the Carrier name simply due to brand recognition from more advertising awareness, not because of actual experience. It is far better to review the manufacturer's consumer record, efficiency of the system, features, and warranty and base a final decision on all these factors rather than name brand recognition. It would be more intelligent and less expensive to operate a higher efficiency system with more features with a better warranty than to pay more for a name. At one level a Toyota and Lexus are the same car but the Lexus costs more because of the name. There might be justification from the consumer because a Lexus has the more elite name and reputation. But nobody sees your HVAC system and do they really care? But many homeowners are stuck in that same mentality of thinking in the name on their HVAC system. At DESCO Energy we stock and distribute five different manufacturers of HVAC equipment. We don't see a worthy difference between any brand at the same feature levels except the wrappers they come in. Name familiarization and recognition isn't a solid basis for selecting a manufacturer because it doesn't provide any real basis for reliability or performance over the long run.
If you want a long lasting heat pump system understanding heat pumps and their features and benefits should help you select the best system for you. All air to air heat pumps operate on same basic principle. In the summer the heat pump removes heat and humidity from the inside of the house and dissipates the unwanted heat outside. In the winter the heat pump removes heat and moisture from the outside air and dissipates heat inside the house. The heat pump uses a compressor and refrigerant to transfer heat from one area to the other through copper tubing and coils. There is an air handler on the inside of the house with a coil and blower as well as electric heat called an air handler or indoor unit. On the outside there is the compressor, reversing valve, suction accumulator, coil and fan called a condensing unit or outdoor unit. Basically the one component that makes the system capable of heating or cooling is the reversing valve. This is the one component that distinguishes a heat pump from an air conditioning system. By reversing the flow of the refrigerant the process of heating and cooling is also reversed. As the outdoor temperature falls in the winter months the efficiency and capacity of the heat pump falls. To compensate for this loss electric heat strips are installed. Electric heat strips are sized according to the heating load of the house because below 30 to 25 degrees the heat pump is no longer effective to operate and the electric heat is now required to provide the full heating load. This is a very basic explanation of a heat pumps operation. For a more detailed explanation of the operation of a heat pump refer to our library section.
Heat pumps don't produce high discharge heating temperatures. And discharge temperatures fall as the outside temperature decreases, opposite of what we really want. Discharge temperatures will range from a high of 95 degrees to 82 degrees. In relative terms 82 degrees may not seem to be a problem until you experience this lower discharge temperature from dry winter air. When the system finally changes over to all electric heat referred to as back up, emergency or auxiliary heat the discharge temperature will elevate to over 100 degrees making the coldest outdoor temperatures more tolerable.
Remember when we said heat pumps remove moisture and heat from the outdoor coil during heating? Because the outdoor coil is colder than the surrounding ambient air it will fall to below freezing temperatures collecting ice below 42 outside air temperatures. As the ice begins to build up it also blocks air flow and continues to build up more and more. If not removed the ice will continue to accumulate until it has built a complete ice ball covering the entire unit in a foot thick ice ball. If left to continue to such a condition the ice will bust the copper coil, destroy the condenser fan motor and compressor causing a total failure of the system. To alleviate this problem the system will reverse it's heating cycle to a cooling cycle defrosting the accumulated ice formations. This defrost cycle can be adjusted to effect itself every 30, 45 or 60 minutes of operation. If a heat pump is left to run continuously only to reverse operation during the defrost cycle, most heat pumps will not properly remove the ice formations and will continue to accumulate causing coil damage. To alleviate this problem the heat pump should be controlled form a hi tech thermostat accompanied by an outdoor thermostat that turns the heat pump off below the balance temperature which is generally 35 to 30 degrees outside temperature. This problem is more likely to occur when the heat pump is undersized or is not accompanied with an outdoor thermostat. Original heat pumps all had outdoor thermostats. To cut costs most manufacturers have made tem an option. We recommend you make it a requirement of your heat pump if you live north of Georgia. Also as the heat pump defrosts the moisture or condensate removed must be allowed to drain freely away form the condensing unit. To do this heat pump risers should be installed which are provided to raise the height of the heat pump allowing free drainage of the moisture. The pad under the heat pump should also be slightly tilted away from the house to also assist in proper drainage. In addition if you live in a snow area the risers should be higher. Remember to remove any accumulated snow away from the heat pump. If you do not have an outdoor thermostat to shut off the operation of the heat pump below freezing conditions and you live in a snow prone area at least turn the heat pump to emergency heat position during the course of any snow storm. This will turn off the heat pump and revert the system to electric heat operation.
In snowy colder climates heat pump compressors can be under tremendous strain during start up. Heat pumps with Expansion or txv valves also take longer times to equalize internal refrigerant pressures. Compressors straining under cold unequalized pressures will stall if operating cycles have short off cycles. You will most likely not be aware any problem is occurring as the compressor is under continuous strain and shuts off on internal electrical protection similar to an automatic resetting circuit breaker. The internal over limit protection trips in this condition when it senses excessive current caused by excessive start up torque or time. The compressor will continue to exceed it's limits as it continually attempts to start. If the compressor fails to start and indoor temperatures continue to fall he system will simply use the electric heat. To alleviate this potential problem a hard start kit is recommended. A hard start kit gives the compressor extra boost to start under hi torque conditions that can be caused by cold outdoor temperatures, unequalized pressures on TXV systems and low voltage brown outs which can occur anytime of year. Hard start kits used to accompany all original heat pump designs but like the outdoor thermostats have been eliminated.
HVAC manufactures also bring certain problems on themselves in heat pumps by eliminating what we consider essential components of any heat pump. The manufacturer can argue that outdoor thermostats and hard start kits aren't required in moderate climates such as Florida or Georgia so why do we need to add the component on every system? And when one manufacturer starts to cut corners the rest follow suit in the name of competitiveness. SEER - Solutions for Energy Efficient Results recommends the addition of outdoor thermostats and hard start kits for any heat pump installed north of Georgia.
Variable Speed Motors

ECM Electronically Controlled Motor or variable speed motors, all manufactured by General Electric for every HVAC manufacturer, are without doubt the best and most misunderstood feature of any system. Misunderstood by contractors due to lack of knowledge and experience, this same misinformation has been passed on to homeowners. Most mistakenly believe the ECM motor varies the speed of the blower motor to change air output from the blower as the need for heating or cooling changes. If you need more heat the blower motor increases the speed of the blower and vice versa. This is not what an ECM motor does. Contractors generally explain the advantages of ECM motors as quiet and inexpensive to operate. Although these are benefits of the ECM motor the primary purpose is to provide constant air flow. To understand ECM motors they should be called constant air flow motors instead of variable speed.


Conventional fixed speed system shuts on and off at full output only
- Uses more energy
- Creates uncomfortable temperature swings
- Produces hot and cold spots
- More contaminants in air due to less filtration
- Reduced humidity control
|
|
Advanced variable speed system runs continuously adjusting output to match conditions
- Uses less energy
- Ramps up gently eliminating uncomfortable temperature swings
- Eliminates noisy on/off cycles
- Continuous air flow improves filtration and humidity control
- Balances temperatures and minimizes hot and cold spots
|
|
|
An ECM motor provides a variety of functions providing a wide variety of features and benefits for comfort, efficiency and performance. The ECM motors start very slowly increasing speed gradually until after 60 seconds the blower motor is finally at operating conditions. At operating capacity the blower motor maintains constant air volume by monitoring and maintaining a constant energy consumption. Finally when the system powers down the blower motor will slowly reduce speed until off. The ECM variable speed motor is controlled by varying the voltage to the motor to control speed and maintain a constant load on the motor. By monitoring current consumption the ECM controller varies voltage to maintain a constant wattage or energy consumption. This is achieved by using a Direct Current or DC Motor. Inside the motor control is a rectifier circuit which converts the incoming power from AC or Alternating Current to DC or Direct Current. DC motor control is more reliable, less complex and less costly than AC motor control. The electronic control system varies the output voltage to maintain a constant load on the motor. As the constant load is maintained the speed of the motor varies as the voltage changes continuously. An ECM motor is substantially more energy efficient compared to a standard PSC Permanent Split Capacitor, Split Phase Motor or Capacitor Start Motor typically used on blower motors. An ECM motor consumes 75 watts of energy compared to 500 to 900 watts for other types of more commonly used motors. On average that results in a 90% reduction in energy consumption.
Newer design concepts of energy efficient systems demand longer operating cycles so there is a need to make blower motors more efficient. ECM motors consume less energy to compensate for the longer operating cycles.
The features and benefits of the first generation of ECM motors were quiet start, quiet stop and quiet operation. The silent operation was a side benefit but the primary purpose of the ECM motor was to maintain a constant air flow efficiently. Standard motors will produce a wide range of air flow variations by only maintaining a constant speed. Standard motors maintaining a constant speed will produces variations in air flow as changes occur. A standard motor is basically designed to achieve a constant speed at the quickest possible start up period and makes no allowance for the variations that can occur in air systems. Variations in air flow occur due to temperature changes of the air - cooler air is heavier and more work is required to move the air while hot air is lighter and easier to move - or from opening or closing of balancing dampers or on diffusers - or filters and coils as they become partially clogged - restrictions in ducting - zone dampers opening and closing or furniture that is placed over diffusers blocking air flow. All these factors affect air flow. As with all HVAC systems the heat pump air handler needs a constant air flow to operate efficiently regardless of these changes. Variable speed ECM motors monitor their energy usage and keep it constant by changing speed thereby producing constant air flows.
There are limitations to the ECM motor so if there is too much obstruction or if the duct system is sized too small the ECM motor will begin to surge as it tries to exceed it's limitations of control and speed. In heating systems air flow is extremely important to the efficiency, comfort, reliability, performance and longevity of the furnace. As detailed in our duct design section of our library section we stress how critically important sizing of ducts becomes. A residential blower with a specific sized motor can only move a certain amount of air through a specific size duct. The ECM motor will help to compensate for some of the under sizing that may occur but should not be considered a solution to correcting extremely undersized ducting.
Another feature in ECM motors include a dehumidification cycle that reduces air flow 10% providing true dehumidification. Some hi tech thermostats reduce the temperature setting 2 or 3 degrees lower to achieve a false feeling of dehumidification by artificially forcing the cooling system to run for longer periods of time. The lowering of temperature set point will in most instances only create more discomfort. But ECM motors produce real dehumidification by reducing air flow across the cooling coil removing more moisture from the air. This is what we refer to as true dehumidification.
Slower start up of the ECM motor also provides benefits to the cooling and heating cycles of heat pumps in different ways. During the cooling cycle the slower time period allows the cooling coil to reach lower temperatures faster providing better dehumidification during mild summer days. For heating cycles the heating coil has more time to produce heat thereby eliminating cold blasts of air so often accompanied by standard heat pump blower motors.
Life was not always heaven with ECM motors when they were first introduced. Original first generation ECM motors were more expensive and had an unacceptable failure rate. General Electric, the sole manufacturer of ECM motors is a company known to dominate their industries by producing exceptional quality products. General Electric went to work immediately at correcting the problems and failures they encountered from the beginning. Today they produce reliable, quality ECM motors with more features than ever before. For this reason General Electric continues to have high consumer confidence and an impeccable reputation. But as with any problems that occur with new product introductions the bad rumors continue to persist for those HVAC contractors having little or no experience with the ECM motors. ECM motors are only applied in higher more efficient equipment in which many contractors have little or no experience. Often times their fear or negative input are often the result of rumors they've heard or bad experiences from many years ago. Be assured that old rumors and problems of the past seem to never die in the minds of some professionals in the HVAC industry. Whether this is due to the contractors fear of new technology, bad experience or usually rumors, understand that technological changes are not embraced by too many contractors. This is usually due to very limited experience with higher efficiency equipment and more common experience with builder's model systems. New technology comes more of a nuisance to the competitive time factor in installations rather than the benefits to the homeowner.
SEER - Solutions for Energy Efficient Results strongly recommends a variable speed ECM motor for any heat pump. The difference in cost is returned the first year in energy savings. ECM motors increase the efficiency of the heating and air conditioning system. An ECM variable speed blower motor not only saves energy but also increases the air conditioning system Seer rating by one point and increases the HSPF efficiency of a heat pump by .3 to .6 points. By maintaining constant air flow ECM motors prevent destruction to the system caused by variations and moderate lack of proper air flow. More constant air flows mean more consistent equipment operation and consistent comfort levels. ECM motors do have limitations and will surge against too small of a duct system or serious restrictions. The surging is a result of the motor attempting to maintain a balance. If the ECM motor surges the problem is a serious obstruction in the air distribution system due to severe under sizing, severely clogged filters or coils or a severe restriction such as fiberglass insulation that has fallen blocking air flow.
ECM motors can also be set up to provide a trim adjustment of + or - 10% of the required air flow, 30 or 70% of normal air flow for ventilation, dual or quattro air flow settings for 2 stage operation and modulating heat pumps. There are a wide variety of system settings for various air flows for various system capacities available from a single ECM motor. There are presently 3 different horsepower ECM motors for residential applications.
From SEER Solutions for Energy Efficient Results THUMBS UP to variable speed ECM motors. They should be a requirement for any HVAC system you select.
Another important component of all air conditioning and heat pump systems is the compressor. The Copeland Scroll compressor is the number 1 compressor used by most major HVAC manufacturers today. The compressor is the heart of every heat pump. The Copeland Scroll compressor utilizes a more efficient design rather than the typical piston reciprocating compressors. Because of it's efficient operation, proven 15 years of reliability the scroll compressor now dominates the entire HVAC market. The scroll compressor is not only efficient but much quieter than previous reciprocating compressors.
With HVAC manufacturers using the same components today for all their systems is there really a big difference between manufacturers? With blower motors using variable speed all made by General Electric, scroll compressors mostly made by Copeland and reversing valves, copper tubing, aluminum fins and contactors and relays all supplied by a few manufacturers there is no real difference between manufacturers except in terms of price, support and warranty.
Important Rebates & Tax Credits
New legislation passed into law effective for 2006 provides tax rebates for high efficiency furnaces. The basics of this legislation provide for any ultra efficient furnace installed after December 31, 2005 is eligible for up to a $200 tax credit. The furnace must have an efficiency of 95% or greater to receive a $150 rebate. If the furnace has variable speed it is eligible an additional tax credit of $50 for a total $200 tax credit.
There are tax credits available for higher efficiency split heat pumps and air conditioners with a 15 Seer efficiency rating and 9.0 HSPF for heat pumps or 14 Seer for packaged systems. Tax credits of $300 are available for these systems.
In many areas utilities may offer rebates for higher efficiency equipment. Check with your local your local electric utility for possible rebates on heat pumps.
Indoor Air Quality
Essential air filtering required.
Earlier we talked about the need for proper filtration for the new hi efficiency heat pumps and the need for proper air filtration. When installing any new hi efficiency heat pump a high media filter should be installed. Any dirt bypassing fiberglass filters will catch and build up on the surface of the indoor coil. Hold up any fiberglass filter to light and you will see how easy dirt can bypass the filter. Perhaps in one month this amount of dirt may not seem significant but after a few years this cumulative dirt becomes excessive. Also look at the air registers or diffusers and see the dirt that has collected. This is dirt reflective of a poor filtration system. Eventually this dirt will completely destroy the heat pump. First it will block the air flow, diminish the efficiency of the heat pump and if left unchecked will destroy the compressor. SEER strongly recommends installing a new high media filter for any new heat pump replacement or installation.
Electronic air cleaners can also be very effective at protecting the heat pump however the reliability factor needs to be taken into consideration. Electronic air cleaners are prone to failure and reliability still remains a problem. When electronic air cleaners fail without warning they also destroy the heat pump by allowing unclean air to clog the furnace coil.
Humidification
A humidifier should be considered an essential part of any heat pump replacement or new installation. Earlier we highlighted the problem of the low discharge air temperatures common to heat pumps. Also the discharge temperature decreases as the outdoor temperature decreases increasing discomfort. Cooler direr air as the outside air temperature decreases is not conducive to indoor comfort.
Humidifiers are an essential requirement for health, saving energy and protection. Humidifiers add precious moisture to dry winter air. Cold winter air is dry indoor air wherever you live. Even though the weather forecast says the outside air is high relative humidity remember the all important word - relative. Relative means the humidity in the air is the amount of moisture the air can absorb at that specific temperature. Colder winter air is incapable of holding a lot of moisture in comparison to warm summer air. As the winter air is heated to room temperature the relative humidity decreases rapidly. The effect is rapid evaporation of the skin from normal body perspiration. Dry winter air feels colder because it has a higher capacity to absorb moisture from the skin. Not only does the air feel colder to the skin, it is drier. For this reason a thermostat setting of 72 degrees doesn't feel warm in drier air. This drier air also increases respiratory infections and viruses. As the respiratory system dries out it becomes more susceptible to infections and inflammation. Viruses including flu and colds thrive more in drier air. This is why there is a substantial increase in flu, viral and respiratory infections in the winter months. The cost of losing several days of work due to a viral or respiratory infection that could have possibly been prevented from proper humidification of the air is well worth the investment. But the advantages of a humidifier don't stop there. Besides increasing comfort levels permitting room temperatures to be lowered and increased health, humidifiers also eliminate annoying and potentially destructive static electricity and protect building materials such as hardwood floors, antiques and other important articles made out of wood. There is no other single device you could add to a heating system that would provide as many benefits at such a minimal cost. In summary humidifiers save energy, increase indoor air quality and protect your health and house.
Heat pump humidifiers must be of the electric heated steam generation type to be effective. Bypass and powered filters do not produce anywhere near rated capacities due to the colder discharge air temperatures. Also bypass humidifiers upset heat pumps critical air flow requirements and can cause harmful air recirculation.
Upflow Downflow or Horizontal
Knowing the intended configuration of your indoor air handler is essential. 92% of air handlers are installed in the upflow position where the furnace is placed upright. Air enters the bottom of the air handler and is discharged out the top. Horizontal is with the air handler placed sideways as air flows through horizontally. Horizontal is used when the air handler is in an attic or crawl space. Downflow, a rarely used configuration but commonly applied in modular homes and trailers where ducting is run underneath the house in a crawl space with the air handler in the first floor living area.
Air handlers placed in a horizontal position should have a secondary drain pan. Secondary drain pans provide added protection in the event the condensate line clogs and water overflowing collects in the drain pan and drains past the condensate trap.
Important Accessories
For heat pumps a hi tech thermostat is strongly recommended. A heat pump thermostat providing two heating stages is required. In addition there are thermostats to control the dehumidification of variable speed motors and humidification. Intelligent energy management is a function of hi tech thermostats to efficiently change temperatures during unoccupied and occupied periods with daylight savings time. By intelligent energy management the temperatures are recovered without the immediate need for electric back up heat. Ventilation control to allow continuous circulation of the blower at reduced speeds. Automatic changeover from heating to cooling and many other comfort and energy savings features are available.
To assist in the installation of the heat pumps there are items that can make installations go smoothly. The most noteworthy items are air handler legs, isolation pads, filter racks and return air plenums referred to as labor savers. To learn more about these items see the complete list under accessories and ducting.
In summary SEER recommends six important components for every heat pump application - risers for the outdoor unit - outdoor thermostat - hard start kit - variable speed blower motors - hi tech energy management thermostat - high media filter
|